With some optical instruments, characterizing the reflectance properties of component coatings can be critical to ensuring optimal performance. In this application note, we measure PCBs painted with different black coatings.
Black coatings may be applied to a surface to minimize the reflection of light from the surface. For example, in the case of an optical bench in a spectrometer, the mechanical housing is often painted black to reduce stray light.
But which black coating to select? Measuring the reflectance properties of different coated surfaces can help in the evaluation. To test this approach, we used an Ocean Optics modular spectrometer system to measure the reflectance properties of PCBs painted with various black coatings.
Background
In theory, a black surface should absorb all wavelengths of light. In reality, there are many variations of black surface coatings with absorbance and reflectance properties that vary as a function of wavelength.
These coating properties are especially relevant in the design of optical instruments, where effectively managing the light in the instrument is vital. For example, in spectrometers, any light that is not absorbed by the optical bench coating becomes stray light that can reach the detector and affect instrument performance. Since the detector cannot distinguish between light transmitted through the sample and stray light created in the optical bench, the presence of stray light limits the maximum absorbance level achievable. As the stray light level increases, the absorbance spectrum flattens until the maximum absorbance value is reached and no further absorption is detected.
To improve instrument performance, stray light can be minimized through the use of absorptive black coatings. Additional optical bench design elements – including low stray light optics and baffles to minimize internal reflection – also are utilized to reduce stray light.
Reflection Measurements
Since most black coatings are not truly black, reflection measurements help to characterize the optical properties of the coated surfaces. The goal of these measurements is to identify coatings that minimize reflection in the wavelength range of interest.
Reflection measurements can be made using a reflection probe, which collects light from the same angle at which the sample was illuminated, allowing it to be used for either specular or diffuse reflection measurements. The standard Ocean Optics reflection probe consists of six illumination fibers around a single read fiber, with a 25° full-angle field of view. Although it may be tempting to connect the 6-fiber leg to the spectrometer, it is more efficient to mate the single fiber to the spectrometer. Each illumination fiber projects a cone of light from the source, all of which overlap at the sample in the center, which is where the read fiber is collecting light (Figure 1).
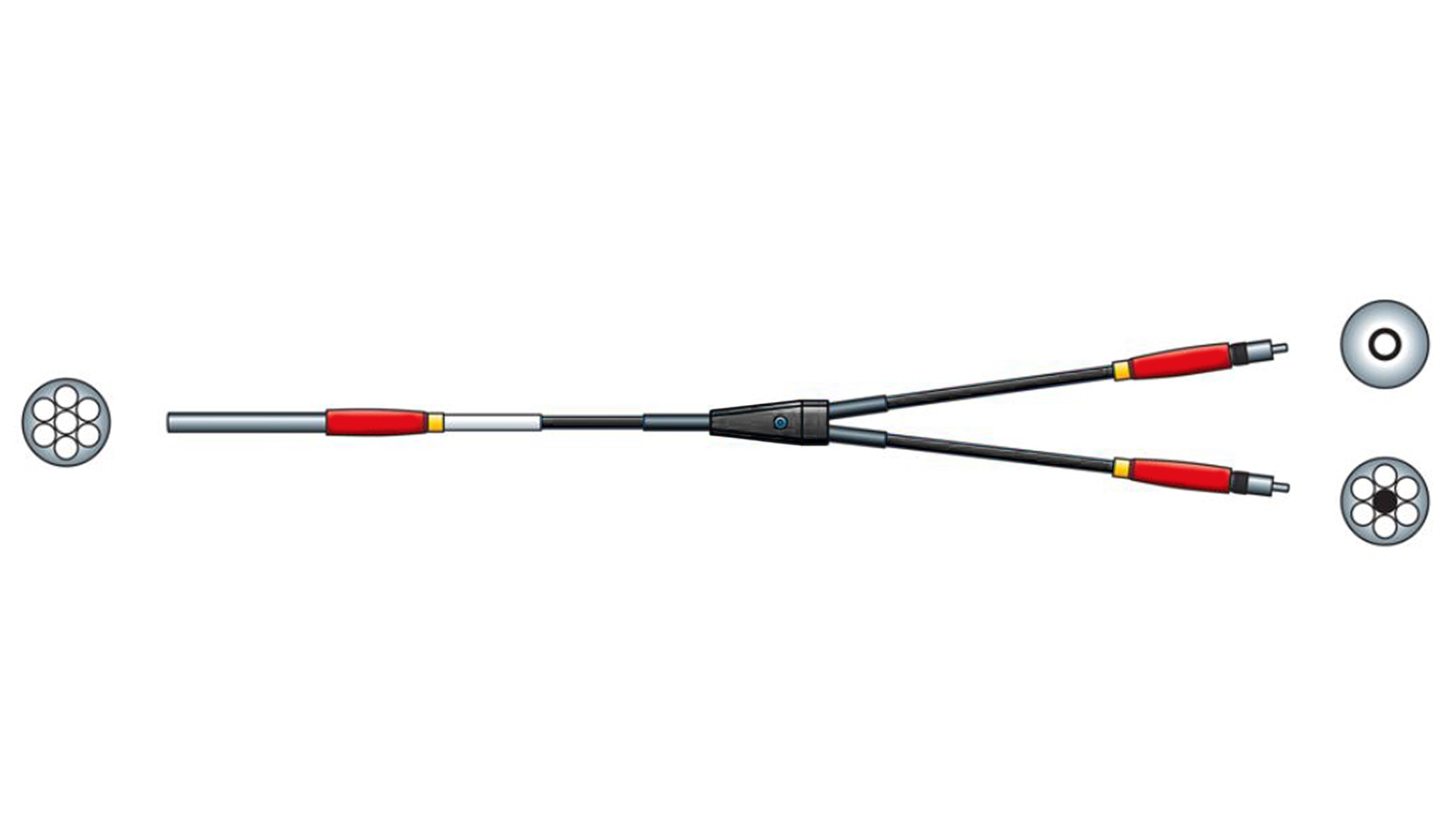
Figure 1. Ocean Optics reflection probes are available in various fiber diameter sizes and optical fiber types (high OH, low OH, solarization-resistant).
To measure specular reflectance, orient the probe at 90° to the sample in a reflection probe holder. For diffuse reflectance, use the 45° port. The reflection probe needs to be pulled back slightly from the surface of the sample within the probe holder, as the rays from the illumination fibers need some space in which to overlap and generate reflected light. The diameter of the sample area will be about half of the distance between the probe tip and the sample (i.e., working at 4 mm away will give you a spot size of ~2 mm). Using a reflection probe holder will ensure a consistent distance from one sample to the next (and when taking a reference measurement). The holder’s matte black finish also helps to reduce ambient light.
When taking a dark measurement with a reflection probe, it is best to block the light at the lamp. Turning the lamp off and then on again will disturb the lamp’s thermal equilibrium, requiring a new reference measurement. If blocking the light is not possible, it is also acceptable to point the probe into a dark space to take the dark measurement, provided there is minimal opportunity to scatter light back into the probe. Resist the temptation to point the probe at something black (like a piece of paper or a cover cloth), as objects that appear to absorb all wavelengths can actually reflect some colors preferentially. The goal is to trap all of the light exiting the probe.
The most important factors in choosing the right reflection probe for your measurement are wavelength range and amount of light needed. System sensitivity should be optimized for the reference standard, as samples are almost always less reflective. Choose your fiber size based on the sensitivity needed, not the spot size desired. The spot size is dominated by the working distance of the probe from the sample and is easily varied. Remember, all fibers have the same 25° full-angle field of view, so a 600 μm fiber has a spot size only 400 μm (0.4 mm) larger than a 200 μm fiber at the same working distance.
Probes with reference legs are available when the lamp needs to be monitored continuously. Additionally, standard or custom expanded wavelength (“mixed”) probes offer multiple lamp input legs and/or measurement legs to allow mixing of different wavelengths and output to different spectrometers for optimization in each wavelength range. For those measuring powders or dense solutions, an angled probe tipped with a 30° window permits the user to immerse the probe directly into the sample and still achieve a consistent working distance.
Measurement Conditions
The reflection spectra for PCBs coated with three types of black paint (flat black, glossy black and black chalkboard paint) were measured using a Flame-VIS-NIR spectrometer (350-1000 nm), HL-2000 tungsten halogen light source and 400 µm reflection probe.
Due to the relatively low reflectivity of these samples, a Labsphere gray-scale standard was used (~20% diffuse reflectivity) as our reference. Integration times ranged from 20-120 milliseconds, with a boxcar setting of 5 and 20 scans to average. A ring stand supported the reflection probe holder for the measurements and a black hood shielded the setup from direct illumination by ambient light. Measurements were made with the probe arranged at 45° (diffuse reflectance) and 90° (specular reflectance) relative to the coated surface using the reflection probe holder.
Results
Although measurements with a reflection probe may seem straightforward, the data can turn up some unexpected surprises. To demonstrate, we looked at three types of black paint: flat black, glossy black, and black chalkboard paint. As shown in Figure 2, the specular reflectance data revealed the chalkboard paint to be least reflective, with the glossy black paint ~10x more reflective. The scale may look a little odd (250% reflectivity for the glossy black paint) until we remember that the reference defined as “100%” is actually a 20% diffuse reflectance standard.
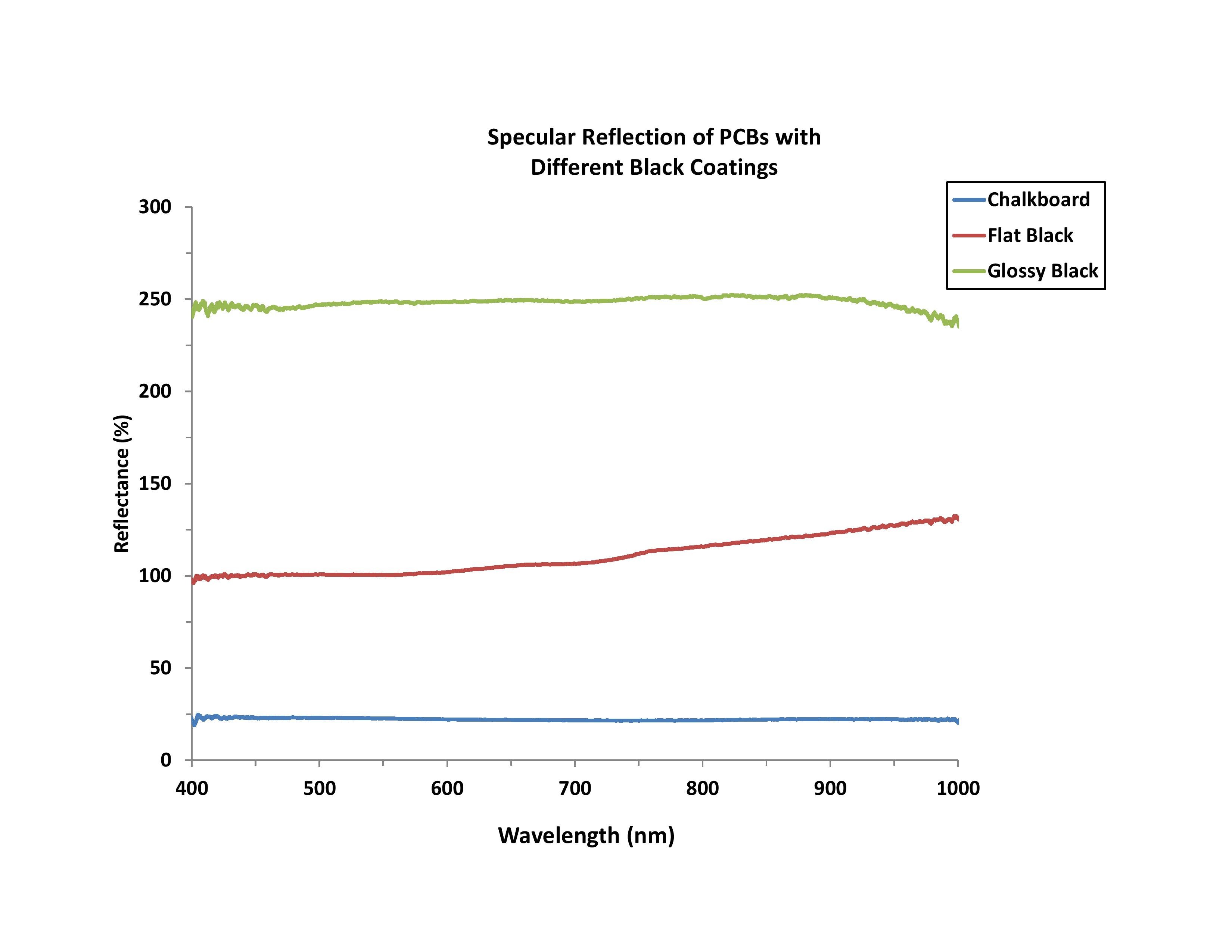
Figure 2. Specular reflectance measurements revealed the PCB with glossy black paint to be most reflective — nearly 10x glossier compared with the chalkboard paint-finished PCB surface.
When examining the diffuse reflectivity data shown in Figure 3, we observe a similar spectral response in the visible range for the flat and glossy black paints. This suggests they would look very similar in color to the eye, even if one of the samples is significantly more reflective.
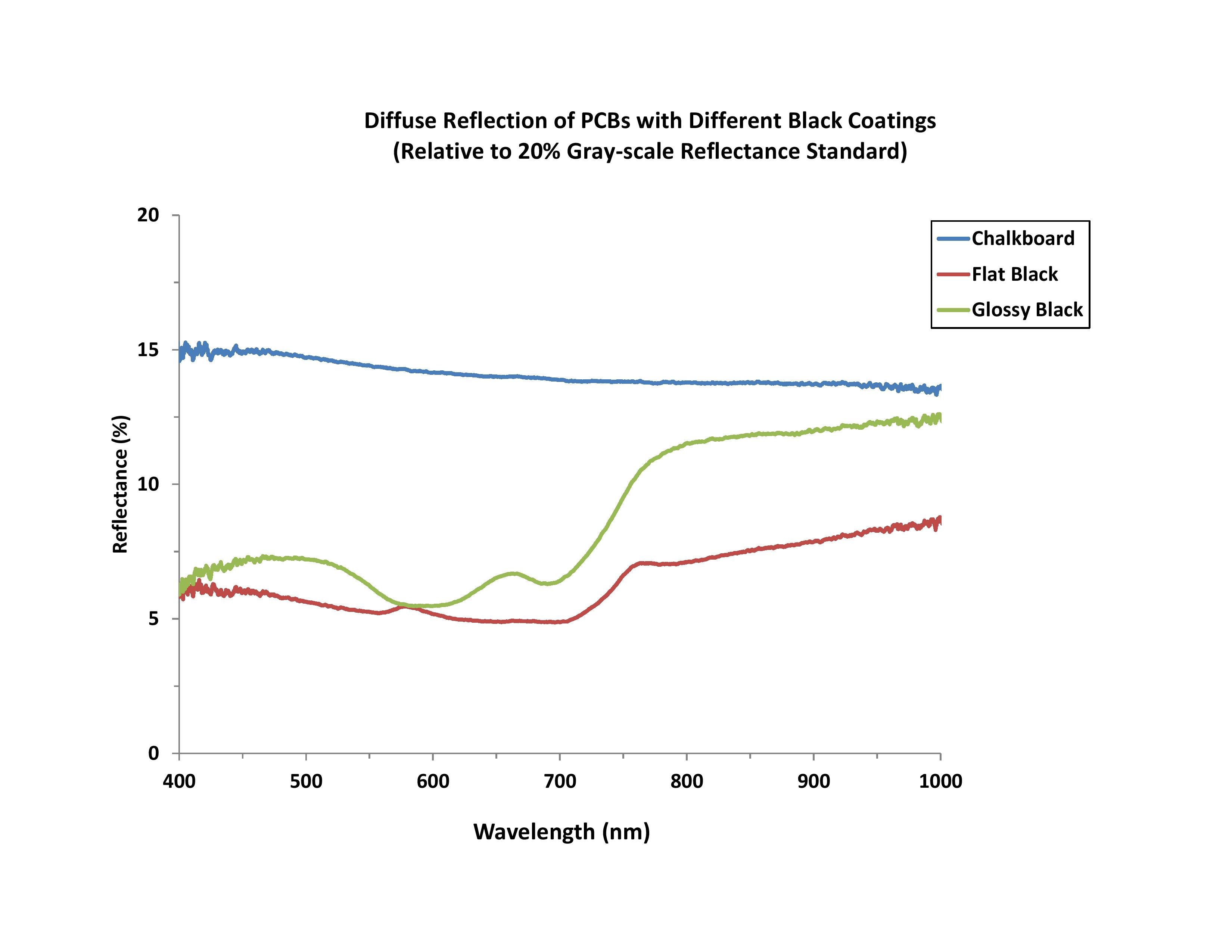
Figure 3. With diffuse reflectance measurements, differences in spectral response for PCBs with different surface coatings become more pronounced at higher wavelengths.
The coatings start to differ in the NIR, which indicates that whatever gives the paint its gloss may be an NIR reflective compound. What is surprising is that the chalkboard paint appears to have a higher diffuse reflectivity than the other black paints. One caveat: The reflection probe is only showing the diffuse reflectivity when illuminated and viewed at 45°.
Conclusions
In this example reflectance application, a simple modular spectrometer setup was used to measure the diffuse and specular reflectance properties of black coatings on printed circuit boards. The spectral data resulting from these relatively straightforward measurements could be used to select the optimal optical bench coating to reduce stray light and enhance instrument performance.
Although we utilized a general-purpose spectrometer and probe-based approach to the reflection measurements, additional modular options are available. For example, we could have swapped our reflection probe for an Ocean Optics integrating sphere, which measures light scattered at 180 degrees from the sample surface and potentially enables more accurate measurements.
On the spectrometer side, our options range from a low stray light spectrometer like the Ocean HDX to industrial-grade instruments including the D8 series color inspection system.
These spectrometers and accessories are part of a much larger range of options for your reflectance measurement needs, with dozens of different reflectance and color measurement configurations possible.